[2024/7/09公開]
Question
自動盤の工具交換作業を効率化する方法はありませんか?
機内の狭い自動盤での工具交換は煩雑で手間の多く時間がかかっています。
Answer
近年普及が進んでいる自動盤用ヘッド交換式工具を使用することで、自動盤での工具交換作業を効率化できます。またヘッド交換式工具を上手く活用することで、機外での工具段取りも可能になります。
自動盤加工における機械稼働率の重要性
加工現場において、生産性の最大化とコスト効率の向上は永遠の課題です。
この目標を達成する1つの鍵は、機械稼働率の最大化にあります。小物の量産加工を行う自動盤においては、機械稼働率の向上はより重要な要素になります。
自動盤加工の稼働率向上のネックとなる工具交換
- 工具交換の煩わしさ
自動盤の機内スペースは非常に狭く、工具交換作業が行いにくい環境です。狭い機内での作業になるため、インサート交換や工具の段取り替え作業は通常の旋盤よりも手間のかかる作業です。
時には、インサートやインサートのねじを機内に落としてしまうなどのトラブルもあり、これら要因が機械稼働率の低下につながります。 - 部品精度の担保
自動盤で生産される品目は主に小物部品になり、その小ささに由来し加工公差も小さくなります。
要求精度が高いことから、高精度な刃先位置調整やテストカットと測定によるオフセット入力作業など精度確保に手間のかかる作業を強いられます。
精度確保の担保のための作業も機械稼働率の1つのネック事項になり得ます。 - 安全性の確保
自動盤加工は、狭い機内や小さな工具により工具交換や段取り作業が難しい環境です。
この困難さから、ホルダの確実な刃物台への取付けやインサートの設置やインサートねじの確実な締付けが行えないリスクを孕みます。
これら作業に不具合があった場合は、加工不良や工具破損などの機械稼働率の低下にクリティカルな悪影響を及ぼすリスクがあります。 - 人材確保の難しさ
近年の労働者不足により熟練工の確保や教育はどの製造現場でも頭を抱える大きな問題です。
可能であれば作業者の熟練度に寄らない方法を確立し、作業の平準化達成が望まれます
自動盤におけるインサート/工具交換作業とよくあるトラブル
- レンチと隣接工具の干渉によりねじを緩める/締める作業が困難
- インサート交換時にねじやインサートを機内に落としてしまう
- 狭い機内でのインサート締付作業を強いられるため、確実にねじを締められない
- ねじのトルクス穴に対し、正しくレンチを掛けられないためねじのトルクス穴やレンチをなめてしまう
- 工具交換時に刃物台に正しく工具を取付けられない
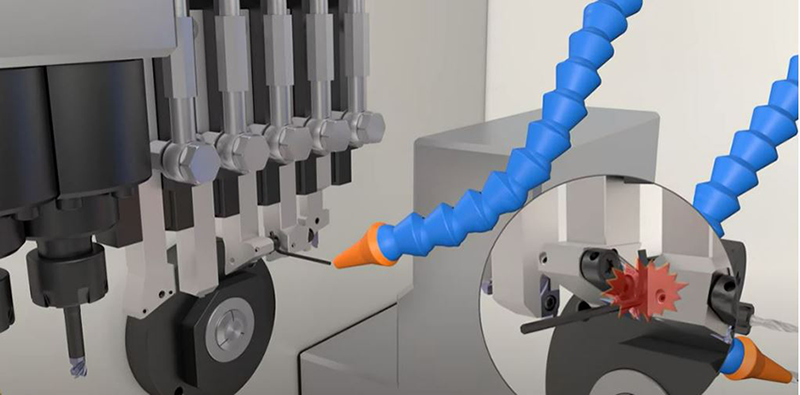
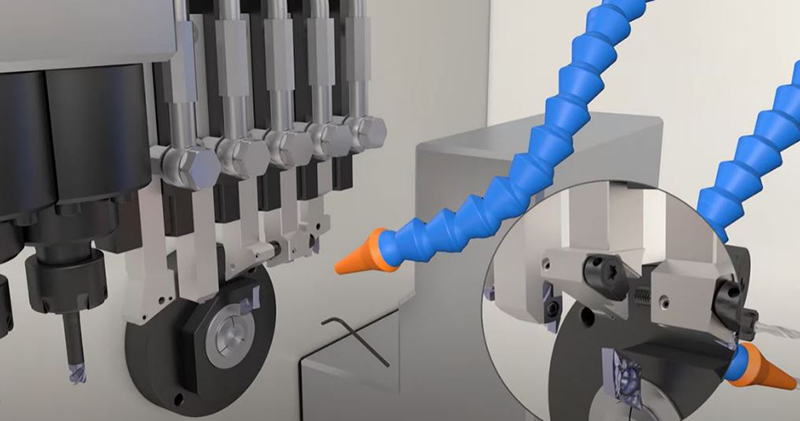
自動盤での一般的な工具交換方法
専用治具とマスターシャンク/マスターヘッドを使った刃先位置の機外計測と補正の方法
計測用の専用治具を準備
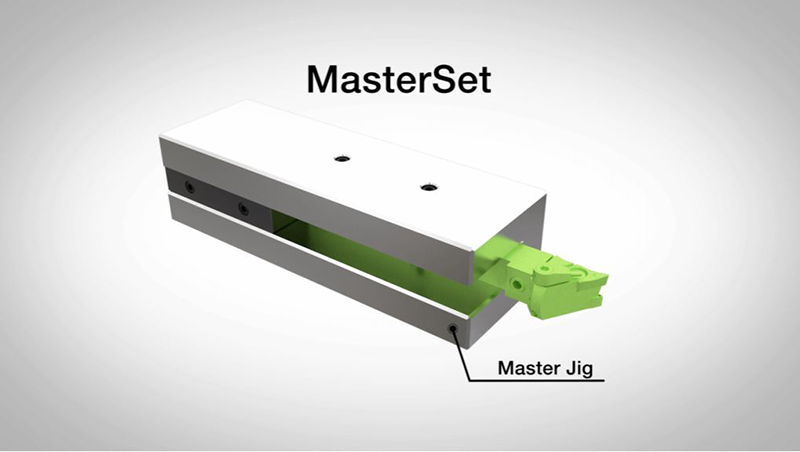
測定の基準となるマスターシャンクとヘッドを定義し、これらを補正入力の基準にする
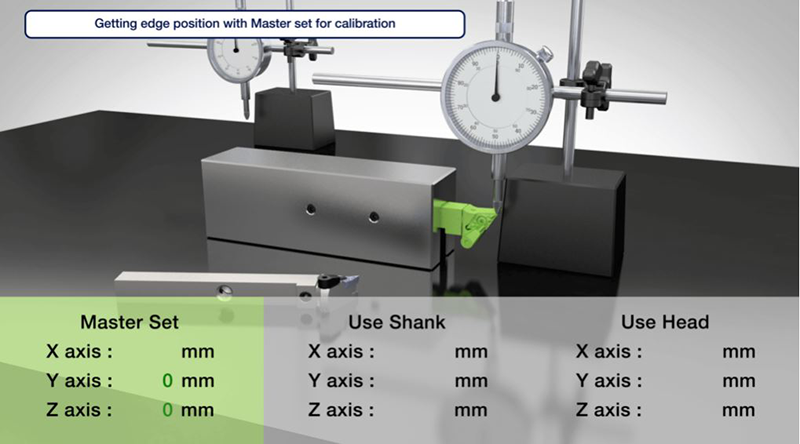
機内に取り付けるシャンクにマスターヘッドを付けて、マスターシャンクと機内取付けシャンクの芯高と径、ワーク長手方向の差分を使用するシャンク毎に計測
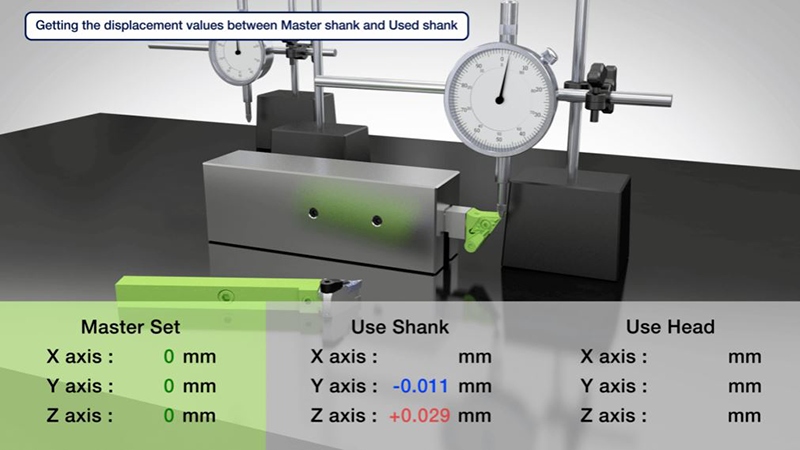
機内で使用するヘッドにインサートを取付け、そのヘッドを計測用治具に取り付ける
取り付けた状態で芯高・径・ワーク長手方向の位置を測定
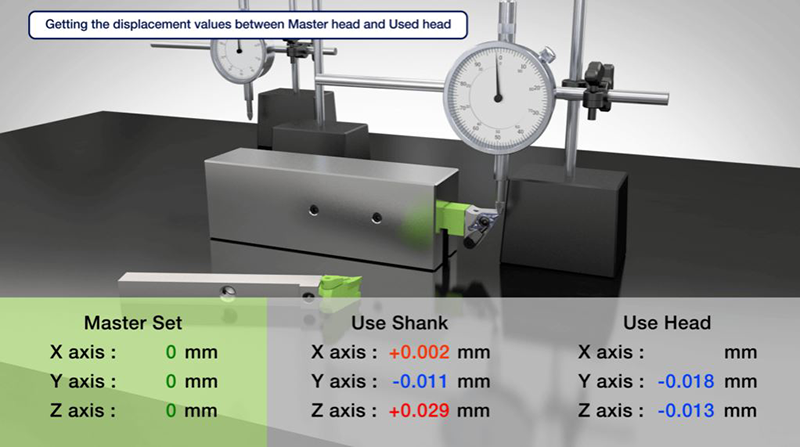
計測した測定値とマスターシャンク間の補正を足し合わせることで、最終的に必要な補正量を定義し、NCプログラムにこれらの補正量を入力。

【動画】自動盤での一般的な工具交換方法
ヘッド交換式工具ModuMini-Turnを使用した機外段取り運用の効果
工具交換時間の削減により機械稼働率が向上
従来10~20分要していた工具交換時間が約3分まで削減。機械稼働率の向上に貢献
熟練度に頼らない作業の平準化
従来方法では、熟練者と新人では作業時間に大きな隔たりがあった。ModuMini-Turnを使用した機外段取りに変更したところ作業時間が同等になり、工具交換作業の平準化が行えた
ミス発生のリスクを低減し、大きなトラブルを抑制。ラインの安定稼働に貢献
機外段取りのため交換作業中の機械操作が最小限に抑制され、入力ミスなどで生じる接触事故発生などの致命的なトラブルを抑制。生産計画に狂いを起こさない安定的な生産が可能になった
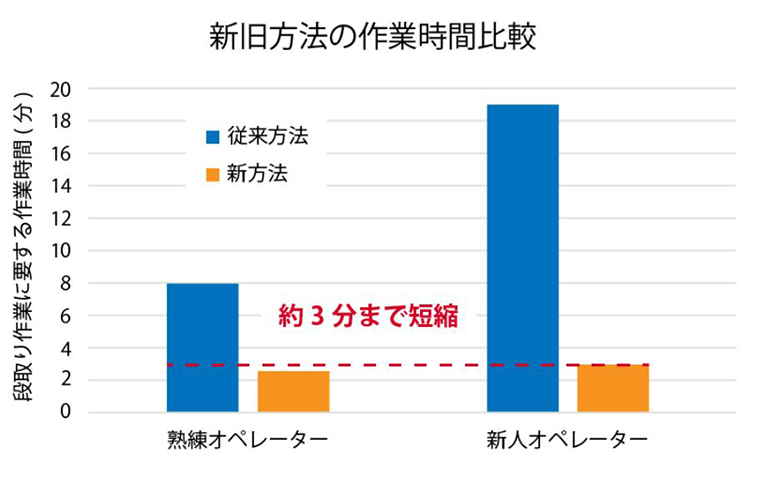
技術情報提供:株式会社タンガロイ