[2024/5/29公開]
Question
製造現場では段取り改善はどのように行いますか?
Answer
段取り改善は各工程の現状の把握をした後で、問題のある工程ごとに改善を実施します。
■ 1. 段取り改善の基本概念とその重要性
■ 1-1. 段取りとは何か?
■ 1-2. 加工工程全体把握する
■ 1-3. 段取り改善の必要性
■ 2. 内段取りと外段取りとは
- 内段取り-工程①機内清掃
- 内段取り-工程②治具取り付け
- 内段取り-工程③ワークセット
- 内段取り-工程③-1クランプ方法
- 内段取り-工程③-2位置決め/芯出し
- 外段取り-工程④加工時間
1. 段取り改善の基本概念とその重要性
段取り改善は製造業において生産プロセスを最適化する基本概念です。これは作業手順や設備配置を効率的に調整し、無駄を削減することで生産性を向上させるものです。効果的な段取り改善により、生産ラインの停滞が減少し、素材の移動や設備のセットアップがスムーズに行えます。これにより、製品の生産効率向上や品質向上が実現され、生産コストの削減と競争優位性の確立が可能となります。製造業においては、継続的な段取り改善が変化する市場に対応し、持続的な成功を確保するために不可欠です。
1-1.段取りとは何か?
段取りは、計画やプロセスを円滑に進行させるための手順や配慮を指します。ビジネスにおいては、効率的な業務遂行やプロジェクトの成功に欠かせない要素です。機械加工においては特に、加工前のワーク/治具の設置を指すことが多く、これにかかる時間をいかに短くして機械の稼働時間を向上させるかが重要視されています。段取りが適切であれば、作業の流れが効率的に進み、リソースの最適利用が可能となります。計画、調整、調整、実行などのステップを含み、円滑なコミュニケーションやタスクの遂行を保障します。
1-2. 加工工程全体把握する
加工工程には多くの工程が含まてれおり、その工程はそれぞれ重要な役割を担っています。
課題を発見する為には、この加工工程を細かく把握し、どこに課題があるかを理解することが大切です。

加工品をつくるには、すべての工程を通らなければなりませんが、生産状況に応じて工程の流れは変わります。
例えば、同じワークを多く作り続ける場合は、ワークの取り外しとワークのセットを繰り返しますが、ワークの形状や加工方法が変更する場合は、ワーク形状や加工方法に合わせて都度治具を変更しなければなりません。
この治具の変更を行う作業を、治具段取りといいます。
治具段取りの作業には、機械テーブルの清掃から始まり、機械テーブルに載せ、治具と機械の主軸が直角及び平行となるように調整し、固定します。この直角及び平行にする調整する作業を芯出し作業といい、高精度な加工において重要な作業となります。

この芯出し作業は、調整と仮締めを何度も繰り返し行い、機械と治具の精度を合致させなければなりません。
しかし、繰り返し行う芯出し作業の間は、機械の主軸を使用するため、加工できない時間(非稼働時間)となります。
加工できない時間は利益を生まない時間となり、この時間が大きく取られることで、結果として生産量が上がらない原因に繋がっているのです。
治具段取り時間の短縮で加工工程を創出!

それでは治具段取り時間の短縮に向けて改善を進めましょう!
1-3. 段取り改善の必要性
製造業において段取り改善は至上命題です。適切な段取りにより生産ラインの停止時間が短縮され、生産効率が向上します。これにより在庫の削減や迅速な受注対応が可能となり、コスト削減と競争力の向上が期待されます。また、一製品の製作にかかる時間も短くなるため、利益率の向上にも繋がります。更に、品質管理も向上し、不良品の発生を抑制できます。つまり、段取り改善は稼げる加工環境を築くことに繋がっているのです。そのため、継続的な改善は市場変化に適応し、迅速かつ柔軟な生産体制を築くために不可欠だと言えます。
2. 内段取りと外段取りとは
内段取りとは、加工機内にて行う段取りを指し、外段取りとは、加工機の外で行う段取りのことを指します。
内段取りは機内で行うため、その最中はどうしても加工が止まってしまいます。
機械の停止時間をなるべく短くするためにできる改善の一つに、クランプ方法の見直しがあります。真空チャックの導入やワンタッチでクランプできる治具を用いることで、クランプにかかる時間が短くなり、ともなって機械停止時間も短くすることができます。
治具段取りの作業には、機械テーブルの清掃から始まり、機械テーブルに載せ、治具と機械の主軸が直角及び平行となるように調整し、固定します。この直角及び平行にする調整する作業を芯出し作業といい、高精度な加工において重要な作業となります。

この芯出し作業は、調整と仮締めを何度も繰り返し行い、機械と治具の精度を合致させなければなりません。
しかし、繰り返し行う芯出し作業の間は、機械の主軸を使用するため、加工できない時間(非稼働時間)となります。
加工できない時間は利益を生まない時間となり、この時間が大きく取られることで、結果として生産量が上がらない原因に繋がっているのです。
外段取りではすでに機外でワークセットを追えている状態ですが、機内への据付方法を改善することで、更なる生産性の向上が見込めます。
せっかく機外ですでに段取りが済んでいても、据付後の芯出しに時間が取られていては元も子もありません。
位置決めユニットを用いた治具を構築することで、機械の停止時間を大きく削減することができます。
これらの段取り改善を行うことで生産効率が向上し、コスト削減/利益率向上に繋げることができます。
内段取り-工程①機内清掃
前の加工が終わって次の加工に移る際、一番初めに行う作業は機内の清掃です。
機械テーブル上に切粉が残っていると加工不良に繋がりかねないため、非常に重要な工程の一つとされています。この工程を楽にするためには、機内での切粉発生を抑制したり、加工後の断続的な液だれを防ぐといった方法があります。
清掃作業を効率的に終わらせることで、利益を生み出す工程である「加工時間」により時間を避けるようになり、稼げる加工環境を生み出すことができるようになります。
内段取り-工程②治具取り付け
機内清掃を終えたら治具の搭載へと工程が移ります。加工に使用する治具は、加工対象のワーク、加工機の機種により多種多様で、それぞれの条件に見合った治具を用意する必要があります。したがって、治具搭載の改善を行うためには、まずはワークや機械それぞれに対応し得る治具の特長を理解しておく必要があります。

5軸加工機で加工を行う際、ツールと治具の干渉が気になる

マシニングセンタの機械テーブル仕様と既存治具が合わない
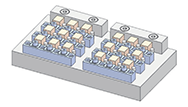
小物ワークの多数個取りの際、治具スペースが足りず困っている
治具の種類は多岐に渡りますが、加工内容に応じてある程度の棲み分けがあり、それぞれの基礎を理解しておくことが、現場での治具改善に繋がります。
内段取り-工程③ワークセット
治具を搭載したらいよいよワークのセットに移ります。治具をワークに搭載し、位置決め/芯出しを行って、ワークをクランプします。このワークセットには、時間がかかるポイントが2点あり、ここが段取り改善のポイントとなってきます。
- ワークのクランプ方法
- 位置決め/芯出しの方法
以下項目にてそれぞれの概要と改善点を見ていきます
内段取り-工程③-1クランプ方法
ワークのクランプ方法も使用する治具によってさまざまですが、物によっては工具の締付に時間がかかったり、調整が必要であったり、何かと手間を取られてしまうことがあります。また、重量のあるワークでは設置そのものが大変になってきます。こういった課題を改善するために、ワンタッチでクランプできる治具や、ワーク設置が容易なバイスなどを用いることができます。

真空チャック導入のメリット

クランプ改善で生産効率アップ!知っておくべき成功事例2

工具を使わずに簡単にクランプがしたい

バイス作業で重たいワークを楽に設置する方法

クランプ締付け力のバラつきをなくしたい
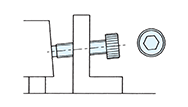
側面クランプ時にワークの浮き上がりが気になる
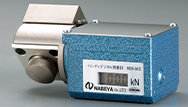
マシンバイス-チャックで簡単に締付け力を測る方法
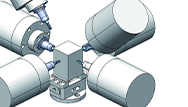
5軸加工機で複数のワークをクランプする方法
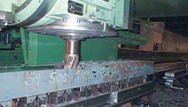
大型加工機での段取りにかなりの時間を要してしまっている

黒皮ワークのクランプ時、ずれや浮き上がりが気になる
内段取り-工程③-2位置決め/芯出し
加工を行う前には、机上でワークの位置を決めて、芯出しを行います。
芯出しとはいわゆる微調整のことを指し、加工前最大の肝となる工程です。
機内での軸に沿って正しく位置が出ているか何度も仮締めと調整を重ねます。
熟練した作業者でもかなり時間を取られてしまうこの工程ですが、できるだけ短時間で終わらせることで機械稼働時間の向上に繋がります。

加工前の段取りにかかる時間を減らす方法を知りたい
精度の良い段取りユニットを用いて位置決め/芯出しが不要な状態を創り出すことで、作業者が変わっても段取りに時間を取られることなく加工が行えます。
外段取り-工程④加工時間
機内で加工を行っている最中は、作業者の手が空く時間となり、この時間で次の加工に向けた準備を進めることが生産効率の向上に繋がります。

加工前の段取りにかかる時間を減らす方法を知りたい
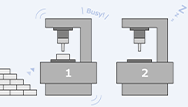
マシニングセンタを専用機として使用する際の機械稼働率が上がらない
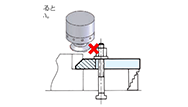
ワーク上面の加工時に刃物と治具が干渉してしまう
ワークセット、位置決め/芯出しを加工機外であらかじめ済ましておけば、機内にセットする際の工数を削減することができます。
また、工程③にて紹介した精度の良い段取りユニットを用いれば機内での芯出し作業が不要になるため、加工の終了後、機内清掃が済んだらすぐに加工を再開することができるようになります。
このような、機外であらかじめ段取りを済ませておくことを外段取りと呼びます。
外段取りを行うことで、機械の停止時間を短縮することができるため、日当たりの加工時間を向上させることができます。
出典:株式会社ナベヤ