KKD(勘と経験と度胸)だけで、設計していませんか? 公差設計のメリット、必要な知識を分かりやすくご説明!
- 公差 / 設計とは?
- 設計現場の実態 / 製造現場の変化
- 公差設計のメリット / 計算事例
今、何が起こっているのか?設計現場の実態!
設計者にとって「公差」は基本中の基本です。しかし、今、その「公差」をもう一度学びなおそうという企業が増えています。
今、ものづくりの現場では何が起こっているのでしょうか?
若手からベテランの設計者に集まってもらい、「公差」について議論を始めると、多くの企業で驚くべき実態が明らかになります。
若い設計者の「公差」に関する知識の絶対的不足と、その事実をベテランの設計者が把握していないという現状です。
若い設計者は、以前の同種部品の公差をそのまま利用することが多く、
全く新しい製品(部品)の場合は、KKD(勘と経験と度胸)で設計しているというのが実態です。
公差設計がベテランの設計者には当たり前のことでも、若い設計者には理解できていません。
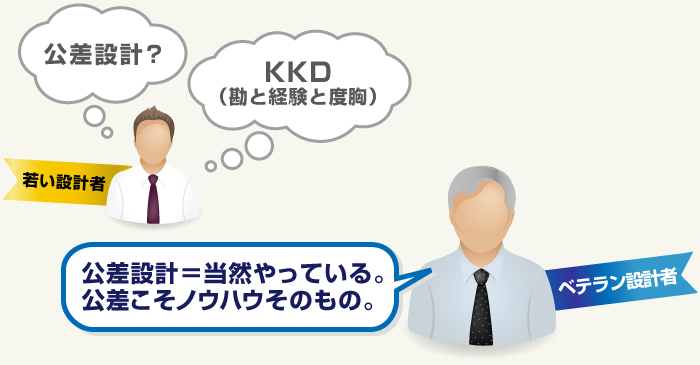
その結果、部品はすべて設計者の指示(設計図面)通りに作られているにもかかわらず、
組み立てられない、あるいは組立後に動作しない、といった事態が多発しています。
つまり、設計者が公差設計を正しく実践できていないのです。
それが、「Fコスト(失敗コスト)の増加」「次期開発商品の遅れ(設計者の手離れの悪さ)」などの悪循環につながっています。
グローバルものづくり -製造現場の変化-
近年において公差の問題が顕在化してきている要因は、製造現場の変化にもあります。
公差設計のノウハウが伝承されず、適切な公差が設定できていない状況の中で、日本が高品質なものづくりを維持できていた鍵は、
日本の製造現場の優れた対応力でした。
海外での生産の場合、これまでのような製造現場の対応は望めず、設計図面の不十分さは、即トラブルに直結します。
それも、出来上がった使えない製品(部品)は、設計図面以上でも以下でもなく、図面通りの製品(部品)であり、
全て設計側にコストとして跳ね返ります。
海外の生産現場でのトラブルは、ほとんどのケースが、「設計図面通りにものを作った結果」なのです。
グローバルものづくりを進め、高品質・低コストを実現するために、基本中の基本である「公差」を学び直し、
図面品質を見直すことが、日本のメーカーにとって急務となっているといえます。