「AIとかIoTというけれど、うちみたいな小さな町工場では無縁の話では?」そう考える町工場の経営者・エンジニアは少なくないだろう。大阪府堺市に、IoT化により業務効率化を果たした小さな町工場がある。精密板金・プレス加工業を営むオシタニプレス工業所では、IT導入補助金(サービス等生産性向上IT導入支援事業)を活用して工場の一部門をIoT化し、今では20代の新人から60代の職人まで、現場でタブレットを操るようになったという。そこでオシタニプレス工業所でのIoTシステムの導入ケースについて、同社の押谷代表と、導入したシステムの開発元であるTranzac株式会社の鈴木社長に伺った。
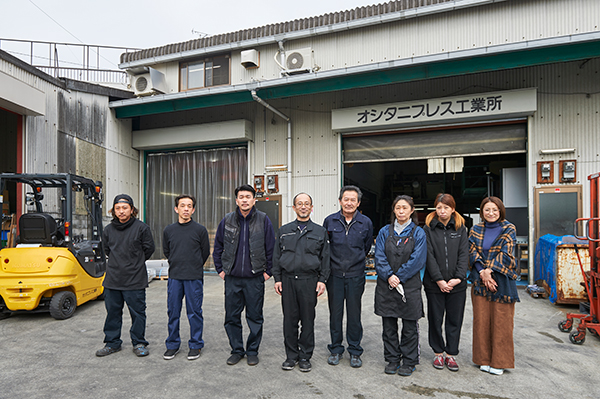
この記事の目次
少量多品種と短納期化…顧客要請で顕在化した生産管理上の問題
MES(製造実行システム)でカンコツ依存した生産管理からの脱却へ
指示書、納品書、受注処理…導入時の目標は「月に6,000枚発生する書類をなくすこと」
現場が自主的に動き始めた
重要なのは幹となるシステムの全体像を作ること
少量多品種と短納期化…顧客要請で顕在化した生産管理上の問題
オシタニプレス工業所が製造しているのは、送風機やチラー、フィルター等の部品。空調機器メーカーの2次、3次下請けが主だ。小型の量産部品から、最大2.5メートルまでの小ロットの板金加工まで幅広く請け負っている。特にプレスと板金を組み合わせたコストダウン提案などを得意としている。


最近の受注傾向として、製造部品の少量多品種化と短納期化が挙げられるという。そのため、時には需要予測し、先行して製造に着手しなくてはならない局面もある。いままで以上に生産管理の重要性が増しているのだ。しかし当時のオシタニプレス工業所は大きな課題を抱えていた。
その課題とは「進捗状況の把握」である。オシタニプレス工業所は板金部門とプレス部門に分かれた工場エリアが1階に、事務所は2階にある。建物の構造上、事務所から現場が全く見えない。事務所にいるだけでは製造状況がわからないのだ。もし進捗を把握したければ工場まで走り「タレパンの右側にあるから穴開けは終わっているな」「ベンダーの右にあるから曲げは全部終わっているな」と現場の状況などから推測していた。もし顧客から問い合わせがあれば現品を探しに工場と事務所を走り回る…こんなことが日常茶飯事だったという。こうした状況のため生産計画もままならないまま厳しい納期の仕事を請けすぎてしまうことが多かった。その結果、現場は過負荷状態に陥ることに。過負荷はそのまま品質に影響を与える。経営者としてはどうしても避けたいことであった。
MES(製造実行システム)でカンコツ依存した生産管理からの脱却へ
導入前のオシタニプレス工業所の生産管理はいわば押谷代表や現場リーダーの「カンコツ」に依存したもの。そこから脱却する方法はないものか、と模索するなかで出会ったのがMES(Manufacturing Execution System)と呼ばれるシステムだった。MESとは製造実行システムと呼ばれるもの。受発注と連携して現場に情報を流すこのシステムを導入することで課題解決のイメージがもてたという。
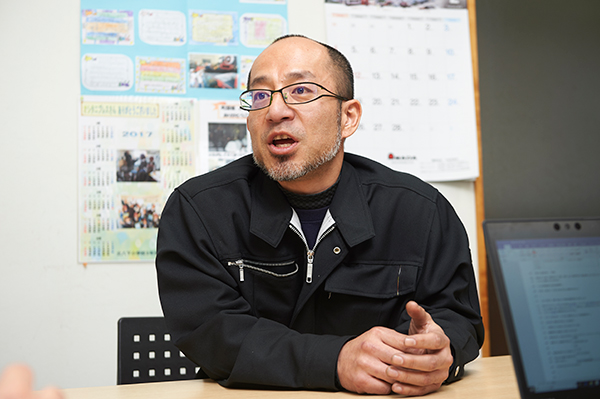
「実は最初からこれ、と思っていたわけではないんです。もともとは製造業向けの一般的な生産管理ソフトを導入するつもりで検討していました。業者さんからは、伝票にバーコードが入るから、入力が楽になると説明を受けていました」。と押谷代表。しかし検討を続けていくなかで、伝票の図番入力が省けるだけで、仕事の進め方は何も変わらないのではないか、と疑問を持ち始めたという。そんなときに展示会で出会ったのかこのシステムだったのだ。
実際に導入したのは、Tranzac社が開発するTranzac MESというシステム。まず受注データを取り込み、AIを使って基準在庫や過去の作業実績のデータ解析を行う。そしてその結果を仕入れや生産計画に反映する。進行状況のデータを収集してそれをクラウド上で蓄積・管理し、AIの解析を経たデータを次の受注状況に反映される。
「実際に現場に受け入れてもらえるかどうかが心配だった」と導入時の不安について押谷代表は語る。「現場と経営者は目線がちょっと違いますから、こちらが良かれと思って導入しても、特に年配の方に嫌がられたりしないか、と」。しかしこの不安は取り越し苦労だったようだ。導入した今では最年長の60代の職人もタブレットを持って現場に入る。タブレットを見て、材料の発注状況や前工程の進捗状況を確認するのが当たり前になった。
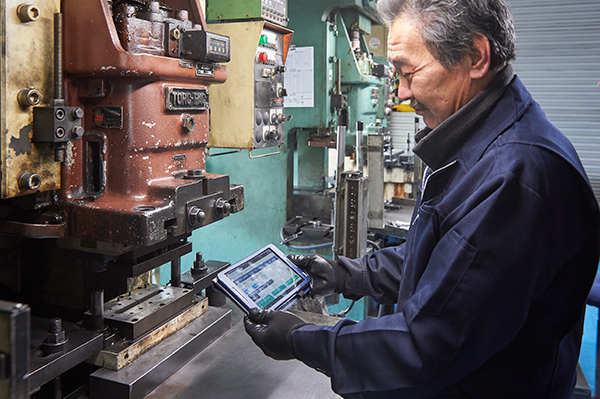
指示書、納品書、受注処理…導入当初の目標は「月に6,000枚発生する書類をなくすこと」
「導入時の目標は、現場から紙をなくすことでした」と導入をサポートしたTranzac社の鈴木社長は語る。ヒアリングを通じて、オシタニプレス工業所では受注処理、指示書、納品書など、毎月約6,000枚の紙を消費していることがわかったという。必要な書類を探すのも苦労する状況だ。そこで事務所から現場に行く情報、現場から事務所に戻る情報を原則データにして、タブレットやパソコンで共有して「見える化」することをゴールに導入作業が進行した。
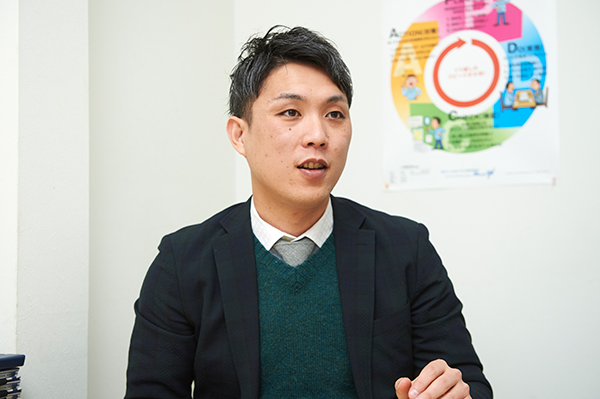
「中小企業にはよくあることなのですが、当初は部品のデータがない状態でしたので、部品の情報をマスタとして登録するのが、本当に大変でした」と鈴木社長。顧客からの発注はFaxやメールなどの注文書に加え「いつものよろしく」という電話オーダーも混在しており、品番を同じフォーマットで整理できていなかったのだ。膨大な量の紙の資料と、押谷代表夫妻の頭の中に分散していた情報を洗い出し入力していった。しかも1つの品番に対して複数の構成部品が紐ついていることが多かったことも困難さの一因となっていた。
現場が自主的に動き始めた
システムが稼働しだすと現場は大きく変わっていった。当初の課題「進捗状況の把握」も改善されていったという。押谷代表曰く「一番大きかったのは、私が生産計画を適切に立てられるようになって、結果として現場の負荷を減らすことができたことです。お客様から引合いがあった時点で、先の生産計画と負荷状況を一覧できるようになったので、お客様と納期交渉ができるようになりました。無理な納期の仕事を受けなくなったので、現場に無理をお願いすることが減りました」。

立てた生産計画はリアルタイムで現場のタブレットに反映される。現場は自分たちの現在のタスクを一覧化し作業に取り組む。導入によって現場で増えた作業は、渡されたタブレット上で作業前に「着手」、終了後に「完了」のボタンを押すことだけだ。
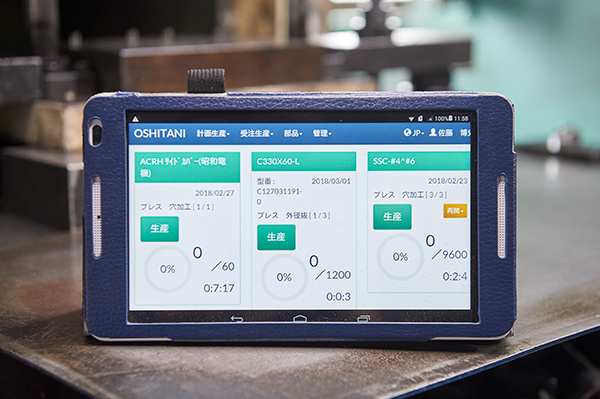
以前の現場では事務所から現場に届く指示書を見ながら「次はどの仕事をやろうかな?」と都度考えて着手していたという。その結果、優先度がうまく伝わらず納期遅れがしばしば発生していた。しかしシステム導入後は現場にも優先度合いが正確に伝わるようになった。しかも現場が納期に合わせて自主的に効率的な生産を調整するようになった。こちらから言わなくても「予定よりも早く上がります」と報告が上がることも増えて、結果として納期遅れもなくなったという。

重要なのは幹となるシステムの全体像を作ること
最後に、約100社もの製造業の現場にMES(製造実行システム)を導入してきた鈴木社長に導入のポイントを聞いた。
「最近『設備にセンサーをつけてデータ取りました』というIoT事例を耳にすることが多くなりました。しかしセンサーがついていればいいというものではないと思うんです。特に中小企業では、センサーで情報を集めてもそのデータを上手く活用できないケースがたくさんあります。大切なのは、センサーがあってもなくても、まず幹になるようなシステムの全体像を作ること。ここがしっかりしていれば、センサーやカメラは必要なところに必要なだけ後付けできるのです」。
今後の計画では、現場が作業前・終了後にタブレットのボタンを押す工程をなくすため、プレス機にセンサーを追加する予定だという。さらに生産完了すると納品書が発行される仕組みの実装や、より工程が複雑な精密板金部門へのMES(製造実行システム)導入などのスケジュールが控えている。従業員がシステムに慣れてきたところで、新しい仕組みを適宜追加していく。幹がしっかりしているからこそ機能拡張計画も立てやすい、といえるだろう。
押谷代表は最後に抱負を語った。
「この先、私たちのような小規模な町工場でもお客様のシステムとの連携を求められていく可能性が出てくると思います。そんなときにも柔軟に対応できるこのMES(製造実行システム)は心強い味方です。自社の成長に合わせて一緒に成長してくれるシステム、身の丈に合ったシステムをパートナーにして、これからもがんばっていきたいと思います」。