最近「IoT活用による生産性向上」が声高に叫ばれているが、中小企業にとっては未だ導入のハードルは高いという見方が多い。なぜならこれまで市販されている「IoTシステム」の多くは「最新設備がネットワークにつながる」というもので、導入コストも数百~数千万円と高額。古い設備には取り付けられないことも多く、大規模な設備投資を伴う大げさな話になりがちだったからだ。
そんな中、「IoTは高いからウチには関係ないと思っていませんか?」と声を上げるのが、自動車部品製造業「旭鉄工株式会社」の木村哲也社長だ。取引先からの増産依頼を機に始めた改善活動をきっかけにIoTを使った「製造ラインモニタリングサービス」を開発し、大きな成果を上げているという。このIoTで、現場が、会社がどう変わったのか?「中小企業こそ、IoTにトライするべき」という木村社長に聞いた。
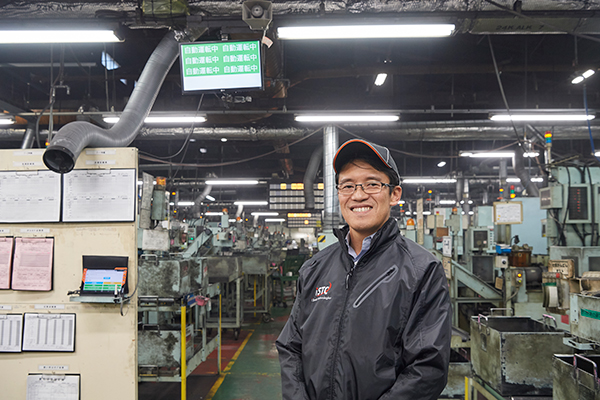
この記事の目次
はじまりは取引先からの増産依頼。「生産個数アップ」に狙いを絞った改善を模索
問題は、見えただけでは解決しない。重要なのはデータを活用した「運用」
改善でなんとテニスコート11面分の土地が浮いた
現場も導入しやすい!自社ノウハウをもとにIoTサービス販売へ
導入3ヶ月で生産量2割アップの事例も。中小企業は生産性向上の余地が大きい
はじまりは取引先からの増産依頼。「生産個数アップ」に狙いを絞った改善を模索
取引先から増産の依頼があったのは2013年のこと。従来のやり方では、増産にはラインの増設で対応するのが一般的だった。しかし、資金的にも工場のスペースにも限りがあって設備投資が難しかったため、既存設備を活かしたまま、改善により生産性を上げる方針に切り替えた。ゴールは「生産個数を上げる」こと、ひとつに絞ったそうだ。
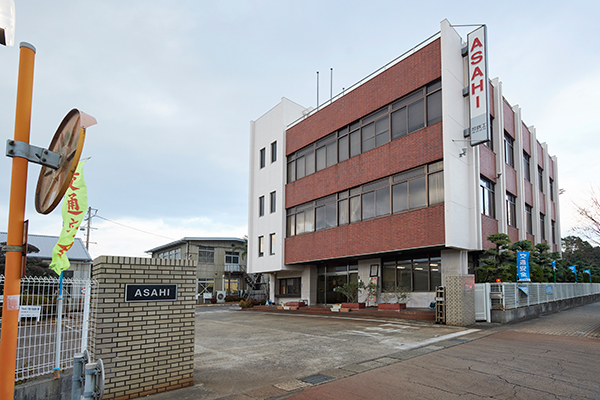
時間あたりの生産数を上げるためには、設備の停止時間と、1個あたりの製造時間(サイクルタイム)を短くすればよい。そこで木村社長は、「時間あたりの生産個数」、「設備の停止時間」、「サイクルタイム」の3点を正確に把握する取り組みから始めることにした。しかし簡単には進まなかったという。
まず、生産個数の把握に関しては、製造担当者が「生産管理板」という掲示板に生産個数と停止時間を手書きしていた。しかし作業員の中には複数のラインを掛け持ちする人もいて、時間ぴったりにすべての機械のカウンターを読むことは物理的に不可能。さらに作業の合間に記入していたため、記入漏れやミスも多く、正確な数値は得られていなかった。設備停止時間やサイクルタイムについても、正確に把握するのは大変難しかった。作業員以外の人間が機械に張り付いてストップウォッチで測定すればいいのだが、この方法では正確な数値が得られない。そもそも貴重な人員を一人割り当てて24時間計測すること自体非現実的だ。そこで木村社長が思いついたのが、当時話題に出始めていたIoTの活用だった。
早速IoTシステムを検討するため展示会やセミナーを回ってみたという木村社長。しかし世に出回っているシステムは「大がかりで高額」「古い設備には取り付けられない」「欲しいデータが見えない」などの問題があると感じたという。そこで「世の中に欲しい物がないなら作ろう」と、木村社長が自ら旗振り役となり「自分たちが欲しいシステム」を開発する取り組みを始めた。システム開発を進めるにあたり、木村社長が決めたのは「けがをしなければ何をやっても良い」というルール。そこでスタッフは「まずやってみて、良かったことを残していく」方法で試行錯誤を繰り返し、システムを作り上げていったそうだ。
例えばシグナルタワーから正常・異常の信号を取るために、3Dプリンタで作った部品を取り付けて、配線を改造して信号を取ってみた。動き自体はうまくいったものの、部品を作るのに時間がかかりすぎたことに加え、設備側を改造するとトラブル発生時にラインの生産が止まってしまうことに気づき、リスクが高いと判断。この反省からデータ取得の方法を、設備に割り込まない後付けセンサに限定することにした。木村社長は自ら東京・秋葉原にも出向き、センサを何種類も購入して持ち帰って新旧さまざまな機械に装着してみたという。シグナルタワーのある設備には1個50円の光センサを両面テープで取り付けて、正常・異常の信号を無線で送信。シグナルタワーがない設備では装置の扉や排出部に1個250円の磁気センサを装着して、部品が1個出来上がるごとにパルス信号を送信するようにした。こうして各機の生産データを工場内にある無線LANを通じてクラウドに蓄積し、工場中の生産状況をリアルタイムで把握できるようになった。旭鉄工オリジナルのコストのかからない「お手軽IoT」のはじまりだった。
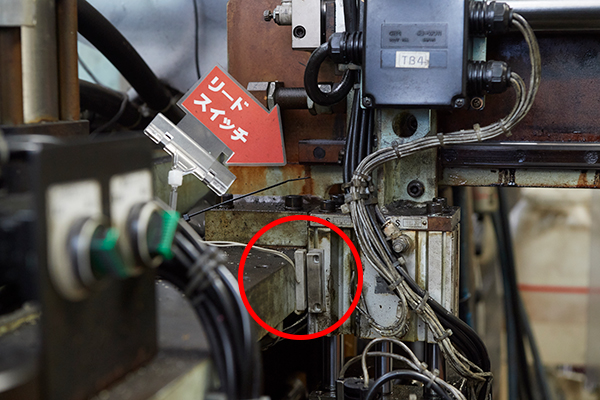
問題は、見えただけでは解決しない。重要なのはデータを活用した「運用」
そもそもIoTの基本は、さまざまな機器をネットワークでつないで情報を集めて「見える化」するところにある。しかし木村社長は先行のIoT導入事例を見て、データを取ることに満足してデータを活かせていない工場が非常に多いと感じていたそうだ。木村社長はこれを「データの貯める化」と呼ぶ。旭鉄工では「貯める化」にならないように、データの素早い運用・活用に徹底的にこだわっている。「IOTで見える化したデータは、ただ貯めていってもデータに埋もれていくばかりで使えません。そこで当社では毎日現場でラインストップミーティングを行って、その場で解決します。」と木村社長は語る。
旭鉄工のIoTシステム運用の象徴ともいえるラインストップミーティングは、毎朝関係者が現場に集まって行われる。その時間までに得られたデータをもとに、「ライン停止の原因は何か」「それは誰がいつどのように対策するのか」「実施済みの対策の効果はどうか」「再発はないか」「サイクルタイムをもっと短くする方法はないか」などを徹底的に議論する。導入当初は問題が多すぎて毎日2時間以上かかり大変苦労したそうだが、2年ほど経った今では改善が進み、5分程度で済むようになった。今では現場の担当者も「3日前の古いデータなんて要らない」というくらい、データの鮮度を重視するようになってきた。
「見えない問題は解決しないので、見える化は必要です。しかし見えただけでは解決しないことも事実。だから旭鉄工では「IoT=IT+OT(Operation Technology)」、つまりITとオペレーション(運用)の組み合わせこそがIoTだと考えています」 IoTを使って集めたデータをもとに「どのように課題を解決するか」「どのように運用していくか」を考えるのは人間の仕事というわけだ。
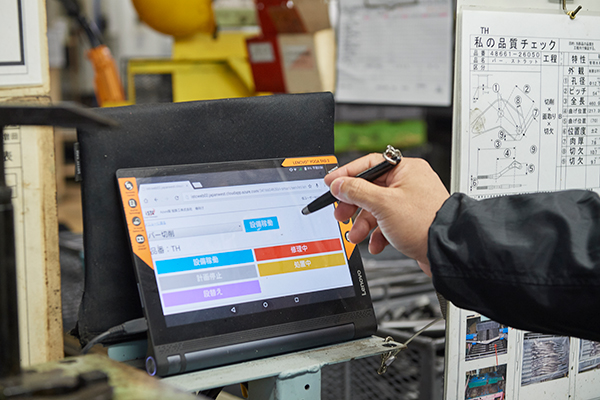
改善でなんとテニスコート11面分の土地が浮いた
さて、IoTを導入し、得られたデータをもとに工程のムダを徹底的に洗い出し、改善したことで、「生産数を上げる」という当初の狙いを達成することができ、他にもいろいろな成果が見えてきた。
増産対応のための2ライン増設の要望が出ていた「牽引フック」のラインでは、サイクルタイムを26秒から17秒に縮め、停止時間も削減できたことで、当初1時間あたり106個の生産量を180個まで引き上げることができた。これにより、2ライン増設の設備投資費用1億4,000万円と、約100m2の工場スペースが不要になった。結果、設備投資をしなくても増産要請に応えることができた。
そこで同様の取り組みを全社に横展開したところ、当初計画があった設備投資を3.3億円抑制。また、工数が大幅に削減できたことにより残業と休日出勤が減り、労務費をなんと年間1億円以上削減できた。ライン増設の回避と余剰ラインの撤去によって3,000m2もの省スペース化が実現できたという。3,000m2といえば、テニスコート11面分以上の広いスペース。これほどの効率化ができたのは、システムを導入しただけで満足することなく、得られたデータを即時活用して改善を繰り返したからにほかならない。
現場も導入しやすい!自社ノウハウをもとにIoTサービス販売へ
「社内でこんなに大きな成果が出るなら、他社のお役にも立てるかも?」と考えた木村社長は、2016年9月に「i Smart Technologies株式会社」を設立。旭鉄工での成功例を元に開発した「製造ライン遠隔モニタリングサービス」の販売に着手した。
同社の「製造ライン遠隔モニタリングサービス」は、設備に後付けするセンサと、送信機と受信機、クラウドシステムのパッケージ。スマホやタブレットなどのデバイスは汎用品を使い、生産個数、停止時刻、サイクルタイム、過去の履歴等の生産情報を自動収集して現場で必要なデータを「見える化」する。無線通信のため配線工事も不要で、規模にもよるが現場で2時間程度あれば立ち上げが可能だ。
導入価格は1ラインあたりの初期費用10万円から、月額費用19,600円からに設定。残業を3時間ほど減らせば元が取れる計算だ。この金額には「これくらいの成果が出ないようなら入れる意味がない」という考えが含まれている。その裏には「稟議書を書かなくても導入できる価格」という配慮もあった。
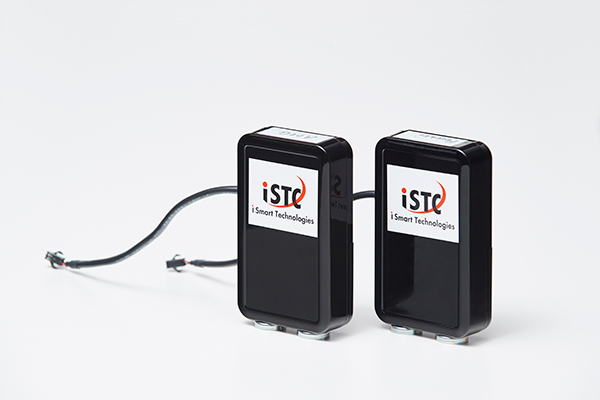
導入3ヶ月で生産量2割アップの事例も。中小企業は生産性向上の余地が大きい
「製造ライン遠隔モニタリングサービス」は、納入を始めた2017年初頭からの1年3か月で約100社に導入された。導入先を見てみると、部品加工業、金型加工業、瓦工場、織物工場、お菓子工場など、業種を問わず広く製造現場に受け入れられているのがわかる。導入先の77%が従業員300名以下の中小企業で、そのうち約半数が100人以下の規模とのことだ。
モニタリングサービスに加えて、2017年12月からは収集したデータを活かすためのコンサルティングを本格的にスタートした。データ収集により問題が「見える化」しても、自力で直せない工場では「貯める化」になってしまう可能性もある。そこで旭鉄工で改善経験を積んだスタッフを派遣し、改善活動になじみのない企業でも改善の効果を得やすいようにした。
遠方のユーザーに対しては、「遠隔モニタリング」の特徴を活かしてリモート会議などを導入し、コンサルタントの訪問回数を極力減らすことで「早く、安く」改善できるように配慮している。いずれの現場でも「コンサルタントがいなくても、現場が自主的に改善できる力をつけてもらう」状態を早期に形成することを目指す。
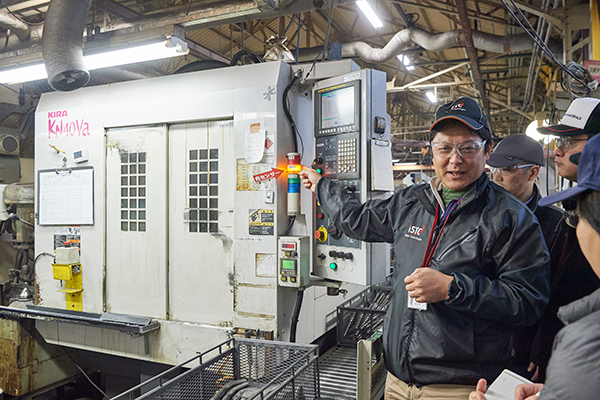
2017年10月に、モニタリングサービスとあわせて月1回のコンサルティングを導入した愛知県の金属加工業者の事例について聞いたところ、わずか3ヶ月で生産数が2割上がったという。この工場では、最初にサイクルタイムのデータを取って分布を見たところ、昼勤と夜勤でサイクルタイムに2割程度の差が見られた。そこで現場で作業員の動きを観察し、早いほうにやり方を統一するなどの改善指導を行った。すると作業員は自分が行った改善を数字で見ることができるようになり、仕事に対する意識に変化が出た。結局現場で自主的に改善が進むようになり、12月の3度目の訪問では生産量が2割程度増えていた。9月までは恒常的に行っていた休日出勤も12月時点でゼロすることができ、働き方改革の面でも成果が出てきたとのことだ。
従来のIoTのイメージから、「小さい会社だから」とか「設備が古いから」という理由で、「うちではまだIoTなんて……」と思っている読者も多かったことと思う。しかし中小企業だからこそ生産性向上の余地が大きく、成果が出たときの設備投資の抑制効果も大きく感じられる。現場でやりがいや働きやすさが向上している点も見逃せない。初期費用10万円から導入できるほど身近になったIoTは、上手く活用すれば中小企業の会社や社員に大きなメリットをもたらすツールになりそうだ。
