中小企業にとっては導入のハードルがまだまだ高そうなIoTシステムだが、最近は低コストで導入できるシステムも登場してきた。そのひとつ、株式会社イマオコーポレーションが提供する機械設備監視システム「ファクトリーステーション」は、無線通信を使って複数メーカーの設備の稼働状況をまとめて「見える化」するものだ。
機械が「稼働中」なのか「停止中」なのか、「停止中」ならば「段取り」なのか「トラブル」なのか。このような情報を当たり前に得られるようになるこのIoTシステムは、現場マネージャーの声から開発が始まった。今では社内外で数多くの工程改善・現場改善を実現しながら、加工現場の負荷を下げるツールとして広がり始めている。
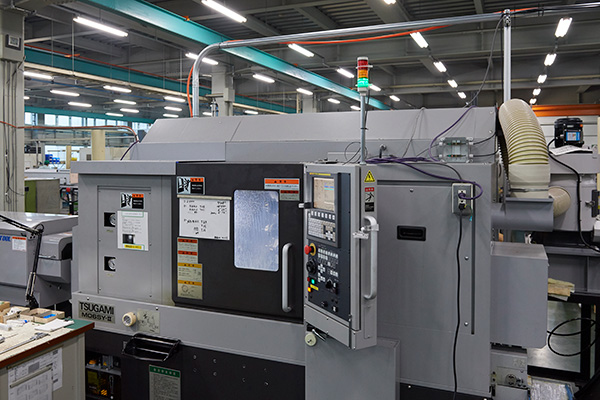
この記事の目次
「機械稼働状況を知りたい」という声から生まれたシステム
全設備にある「シグナルタワー」に目を付けた
稼働状況が見えるようになって起きた「変化」とは?
配線工事不要! シンプルなIoTシステムとして販売へ
「見える化」のその先へーーー続く、広がる現場改善
「機械稼働状況を知りたい」という声から生まれたシステム
機械加工の工場では機械の稼働率が生産量に直結するため、「機械の停止時間をなるべく短くしたい」「停止の原因を正確に把握したい」というニーズがある。しかし実際に稼働状況を把握しようとしても、現場では古い機械も現役で動いているし、複数メーカーの加工機から共通の信号を取るには改造や配線が必要で、なかなか実現に至らないのが実情だろう。
標準機械部品メーカーとしておなじみの株式会社イマオコーポレーションでも、同様の事案が発生していた。機械部品や治具の小ロット加工を行う美濃第2工場では、機械の稼働状況を作業者が日報に手書きして、一ヶ月に一度データをまとめて手集計していた。そんな中で2010年、現場マネージャーが「夜間稼働中の機械の稼働状況を把握したい」と声を上げた。
当時は機械の停止に気付くのが遅れ、問題発生時に迅速な対応ができないことが問題視されていた。さらに手作業によるデータの収集や更新にも時間がかかり、タイムリーなデータ分析や問題発生時の対応が遅れていた。改善のため機械設備監視の導入も検討されたが、コストや運用開始までの時間を考えると導入に踏み切れないという状況だった。
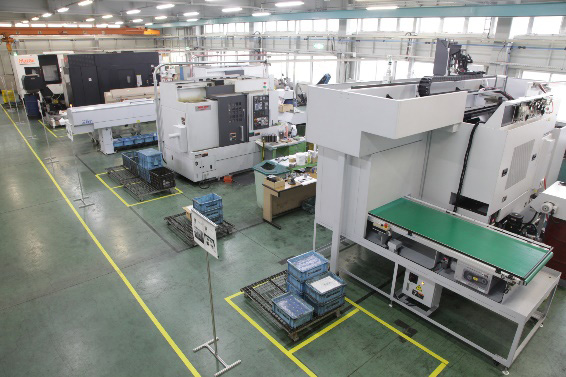
実はイマオコーポレーションは、2008年に同社初の無線通信機器として「メッセージウォッチ」を発売、その後2010年には「シグナルスイッチ」という工場用無線機器も発売していた。先の現場マネージャーの声を受けてスタッフが知恵を出し合ったところ、自社製品の「シグナルスイッチ」を活用してはどうかという案が出た。そこで、美濃第2工場のNC旋盤・縦型マシニングセンターを合わせた7台を対象に、「生産阻害要因を特定して無駄取りを実施する」ことを目標にしたプロジェクトが始まった。
全設備にある「シグナルタワー」に目を付けた
最初の課題は、稼働状況の情報をどのように得るか?という点だ。当初は機械設備から直接接点を取る方法を検討したが、ユーザー側での機械の改造を推奨しないメーカーがあったため見送りに。次に目を付けたのが、全ての設備についていた「シグナルタワー」だった。全ての設備で緑が運転中、赤が停止を示していたので、各機のシグナルタワーに光センサーを取り付けて稼働状況を取得することになった。この方法を採用したことでメーカーを問わず取り付けが可能になっただけでなく、工作機械側の改造が一切不要となり、稼働開始までの時間を大幅に短縮。さらに改造による機械の動作不良など責任の所在を心配する必要がなくなるなどのメリットも生まれた。
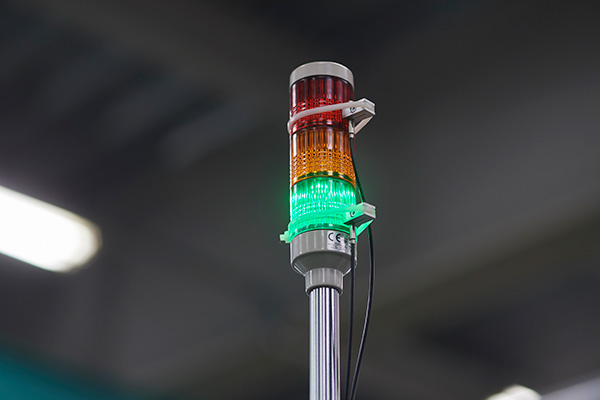
光センサーの選定過程では、市販されていた各社の製品を調達してテストを実施したが、ものによっては西日や蛍光灯の光に反応して正常に動作しないものがあることも判明し、試行錯誤が繰り返された。また、信号の入力方式や無線の通信方式にも様々な検討がなされ、光センサーで集めた設備の稼働情報を「シグナルスイッチ」経由で1台のパソコンに集めて情報を見られる仕組みを作り上げた。まだ「IoT」という言葉が認知されていない2012年のことだ。
稼働状況が見えるようになって起きた「変化」とは?
さて、自前で作りあげた「設備稼働監視システム」で機械の稼働状況をリアルタイムで見られるようになり、また過去の稼働状況データも蓄積できるようになった。これにより、1ヶ月ごとに稼働目標時間との差異を分析し、要因を探って対策できるようになった。段取りに時間がかかっているのか、トラブルが頻発しているのか、といった「生産阻害要因」が見える化できたことで出てきた課題は、イマオ独自の改善活動「VPM活動(*)」に展開されるようになった。システムから得られた情報を、生産性向上を検討するためのベースとして活用する姿勢が社内に定着していった。
※Value Producing Managementの頭文字を取った社内の改善活動。改善事例はイマオコーポレーションのホームページで一般公開されている。
すると現場にいくつかの変化が起こり始めた。
①稼働率の向上
機械停止がすぐにわかるようになったため、問題発生時はすぐに駆けつけて対処できるようになった。結果的にダウンタイムが削減できて、機械の稼働率が向上した。また問題の対処のためにデータを取る意識形成ができて対策への踏み込みが早くなった。
②生産計画の適正化
機械ごとの負荷を具体的に見られるようになったことで、負荷の平準化を図り、適正な生産計画を立てられるようになった。あわせて漠然としたミーティングが減り、データに基づいて具体的に議論できるようになった。
③現場の意識の変化
IoTシステムが「物言わぬ管理者」の役割をして、現場エンジニアは何かあると聞かれる前に自主的に報告するようになった。一方、生産計画の適正化により現場の負荷の偏りが平準化され、エンジニア間の不公平感が減少し、IoTでは「がんばっていることが常に上長に見てもらえる」状況になってやりがいも大きく向上した。
改善・効率化のための設備投資の面でも、想像以上の効果があった。例えば現場スタッフが治具による段取りの効率化を提案する場合、IoT導入前は治具導入による「効率化」「成果」が提案者の予想でしかないため、治具に投資する説得材料としては弱く、なかなか進まなかった。しかしIoT導入後は提案による「成果」を具体的な数字で提示できようになり、上長も「改善の為に必要なコスト」と即決できるようになった。それまでの「感覚論」「予想」から脱却し、データに基づいて改善が具体化してスピードアップできたというわけだ。
配線工事不要!シンプルなIoTシステムとして販売へ
美濃第2工場における成果は社内で共有され、イマオコーポレーションの全工場に導入されることとなった。また、工場見学に訪れたユーザーから「当社でも採用したい」との要望も出たことから、ノウハウを製品化し外販するプロジェクトが2014年にスタート。機械のメーカーを問わず、新旧も問わず、大掛かりな配線工事も不要なシンプルな構成で、工作機械を複数台稼働している工場の管理に向いているIoTシステムとして、2015年には「ファクトリーステーション」の販売を開始した。機能を「設備稼働状況監視」に絞ったシンプルな構成ながら、長距離の無線通信にも対応し、わかりやすいソフトウエアも標準仕様で、導入までの期間も短いなど、現場のニーズと合った場合の導入メリットは大きい。
ここで「ファクトリーステーション」の機能を整理してみよう。
①光センサーで情報収集
既存のシグナルタワーに光センサーを取り付けて、設備の稼働情報の収集を行う。この方法は、対象設備の柔軟性が高く、工作機械に限らず搬送装置、食品機械、検査装置などにも展開可能だ。

②無線通信
無線通信によりデータを集めて稼働状況を一覧できる。通信方式の工夫により、見通し800m先の機械・設備までの監視が可能。
③ブラウザで閲覧できる
パソコン、タブレット等のデバイスで稼働状況をリアルタイム表示。データはExcelやCSV形式にデータのエクスポートが可能で、データの加工も容易だ。
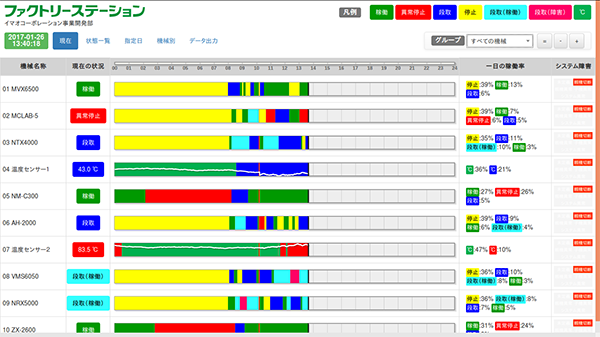
「見える化」のその先へ…続く、広がる現場改善
イマオコーポレーションの社内では、いろいろなデータが見えるようになったことで、管理職も現場エンジニアも「もっと良くしたい」「もっとデータを見たい」と考えるようになってきた。今後は人の動きの情報を取得するマットセンサーの導入や、段取り時間をより詳しく見る仕組みなどを検討中で、さらなる現場改善を模索している。今後も自社工場における改善をモデルケースにして、製品へのフィードバックを続けていくとのことだ。
最近では大手メーカーの小規模工場からの引合い・実績も増えているそうで、シンプルなシステム構成だからこそ導入のハードルが低く、広く受け入れられているといえる。2017年の最新版には、温度、湿度、CO2濃度等のアナログ情報の収集・表示が可能になるなどの新機能を追加し、あわせて自社でIoTを構築したい企業向けに親機・子機の単体での販売も開始した。
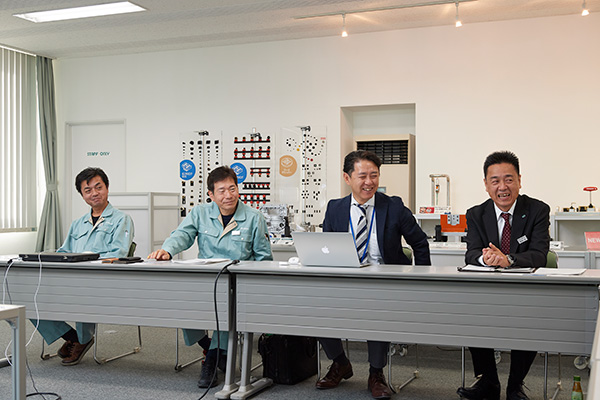
とかく経営側のメリットが取り沙汰されがちなIoTだが、イマオコーポレーションの事例では現場マネージャー、現場エンジニアにとっても大きなメリットがあった。システム導入前は上長に「忙しい」「負荷が大きすぎる」と訴えても伝わりにくかったところ、導入後は生産計画時点で負荷が平準化されるようになった。改善提案も通りやすくなり、無駄に走り回ることも減り、上長に努力が伝わりやすくなったということで、「楽になった」と感じるエンジニアも多かったことと思う。
今回のケースを通して、IoTで集めた客観的なデータは、経営者・管理者だけでなく現場の負荷も下げるという側面もあることが見えてきた。「生産性向上」「IoT」が声高に叫ばれる中、企業にとってもエンジニアにとってもデータという「武器」の活用が、ますます大きな「武器」になっていくだろう。
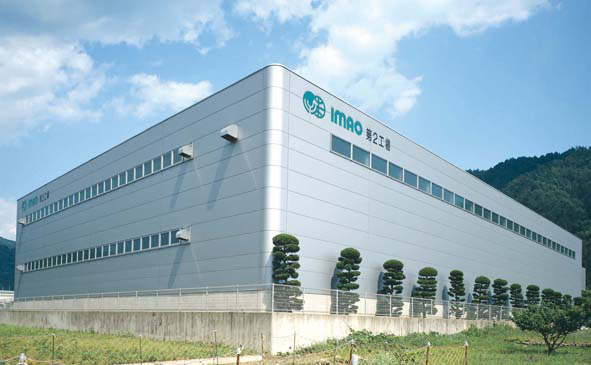