[2024/8/2公開]
Question
ドリルについて教えて
穴あけ加工を行うのですが、ドリルについて選定方法など詳細を教えてください
Answer
ドリルとは、金属などの加工物に穴あけを行う切削工具でキリとも呼ばれます。ドリルはボール盤、旋盤、フライス盤、マシニングセンターなどの工作機械や電動工具などに取付けて、回転させて加工物に穴をあけます。ドリルには先端に切れ刃があり、側面には切れ刃が無いので軸方向にしか加工できません。以下にドリルの詳細を記載していますのでご参照ください。

分類
ドリルには切れ刃からシャンクまで同一母材のソリッドドリル、ボディにチップを取り付ける刃先交換式ドリル、ボディに切れ刃のヘッドを取り付けるヘッド交換式ドリルなどに分類されます。

材質
切れ刃の材質は超硬、粉末ハイス鋼、ハイス鋼などがあります。
切れ刃表面には高硬度・高耐熱のコーティングを施し耐摩耗性を向上したものや、ホモ処理や窒化処理などの表面処理したものがあります。
材種 | ミスミマーク | 材種説明 | 主な被削材 |
---|---|---|---|
ハイス鋼 | ![]() |
高速度工具鋼のことで、JIS表記でSKH2やSKH3などにあたります。鋼にタングステン・クロム・バナジウ ム・モリブデンなどを加えた工具鋼で切削工具に広く使用されています。 超硬と比較して安価で靭性に優れていますが、耐熱性・耐摩耗性は劣ります。粉末ハイスと分けるために溶解ハイス鋼とも呼ばれることがあります。 | アルミ合金 銅 鋳鉄 炭素鋼 合金鋼 |
粉末ハイス鋼 | ![]() |
材料を粉末状にして圧縮焼結させたハイス鋼です。粉末ハイス鋼は粒子が細く結合度が高いため、溶解ハイス鋼に比べて耐摩耗性が高いといえます。また靭性も改善されチッピングが減少します。しかし製作工程が増えるため、粉末ハイス鋼の方が一般的に高価になります。 | アルミ合金 銅 炭素鋼 合金鋼 ステンレス |
超硬 | ![]() |
超硬とは主成分の炭化タングステンをコバルトやニッケルで結合させた材料です。製法は材料の粉体を高圧成形し焼結させます。ハイス鋼に比べ硬度が高く、耐摩耗性に優れています。粒子を微粒子化し硬さと靱性を向上させた超硬をMG超硬と呼んでいます。 | アルミ合金 銅 炭素鋼 調質鋼 ステンレス |
コーティング種類 | コーティング説明 | 主な被削材 |
---|---|---|
鋼用 | TiAlN、TiNなど様々なコートがありますが、基本的な目的は耐摩耗性を向上させることです。ステンレスの加工などコートの有無で工具寿命に大きな差があります。 | 一般鋼 高硬度鋼 |
非鉄用(DLC) | 摩擦係数が低いため凝着しにくいコーティング。硬度は高いですが耐熱温度は低いので、アルミ加工などに適しています。 | アルミ 銅 |
非鉄用(CrN) | 非鉄金属との親和性が低く凝着しにくいコーティング。耐熱温度は低いので、銅の加工に向いています。 | 銅 |
非鉄用(ダイヤコート) | 表面硬度が最も高いコーティング。摩耗が激しいグラファイト加工に適しています。鋼とは親和性があるため使用できません。 | グラファイト アルミ |
ホモ処理 | ホモ処理とは多孔質の四酸化三鉄(黒さび)被膜を施す表面処理で、摺動性に効果があります。 | 一般鋼 |
窒化処理 | 窒化処理とは金属表層に窒化化合物を析出させる表面処理で、耐摩耗性に効果があります。 | 一般鋼 |
選定仕様
ドリルの仕様は主にドリル径、溝長、全長、シャンク径で表します。
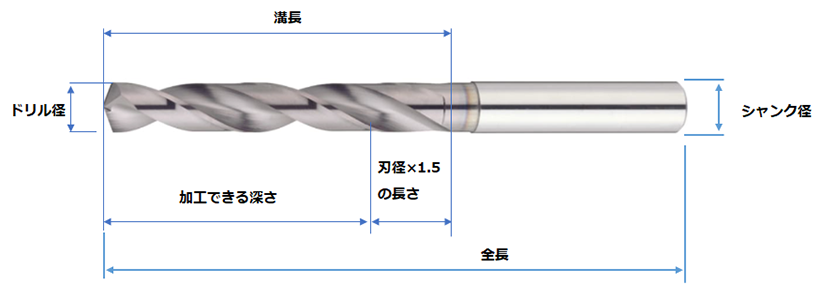
溝長を選定する場合、加工できる穴深さより長い必要がありますのでご注意ください。詳細は以下の技術情報をご参照ください。
シャンク形状はストレートシャンク、エンドミルのシャンク径に合わせたエンドミルシャンク、テーパシャンクなどがあります。

その他の仕様に、シンニングがあります。シンニングとはドリル先端にスラスト(軸方向)荷重を低減させるための処理です。形状にはX型(深穴加工向き)、R型(ステンレス系加工向き)、S型(鋳鉄・非鉄系加工向き)などがあります。
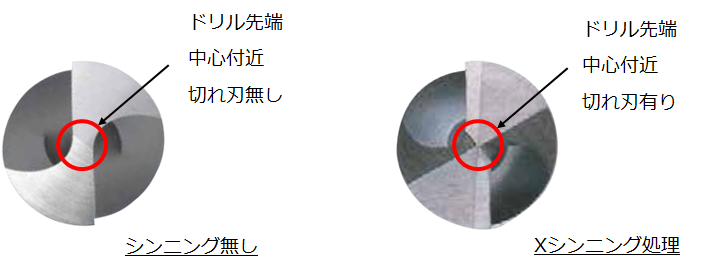
先端角は118°前後が一般的ですが、高硬度の加工物にはやや広い140°前後が適しています。
また曲面への加工が可能なフラットドリルなどもあります。
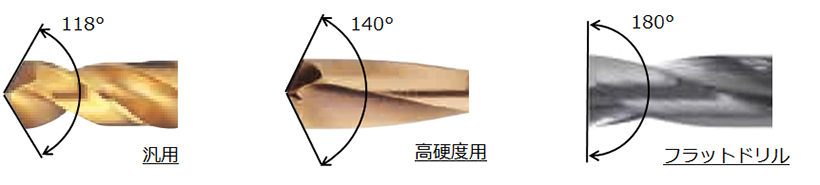
切削条件
ドリルの切削条件は回転速度と送り速度で設定します。
回転速度は切削速度とドリル径から求められます。同じ回転速度でも刃径が小さいと切削速度が小さくなるので、適正な切削速度を保つためにはドリル径の換算が必要となります。切削速度はそれぞれのドリルの推奨値が、被削材ごとカタログに表示されています。
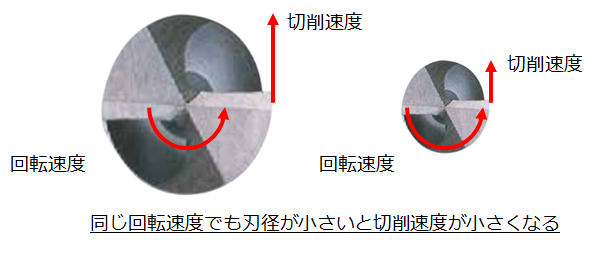
ハイス鋼ドリル切削速度例
被削材 | 切削速度V (m/min) |
---|---|
一般鋼 (SS・SC材) |
25~32 |
合金鋼 (SCM等) |
16~20 |
工具鋼 (SKD, SK, SKS, SUS等) |
10~12 |
超硬ドリル切削速度例
被削材 | 切削速度V (m/min) |
---|---|
一般鋼 (SS・SC材) |
60~80 |
合金工具鋼 (SUJ 2、SKD11、SKD12) |
40~60 |
ステンレス鋼 (SUS303、SUS304、SUS416) |
25~35 |
調質鋼 (40~48HRC) |
20~30 |
切削速度を回転速度する換算式
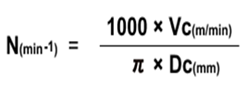
N(min-1):1分あたりの回転数
Vc(m/min):切削速度
π:円周率(=3.14)
Dc(mm):工具径
送り速度もそれぞれのドリルの推奨値が、被削材ごとカタログに表示されています。
通常 単位は1回転あたりの送り量ですので、エンドミル加工の単位時間あたりの送り量とは異なります。工作機械への入力が単位時間あたりの送り量の場合は下式で換算してください。
1回転あたりの送り速度を1分間あたりの送り速度にする換算式
1分間あたりの送り速度(mm/min) = 1回転あたりの送り速度(mm/rev)× 回転速度(min-1)
【穴あけ作業での注意事項】
- ドリルで穴あけ加工をする前に、スポットドリルなどでもみつけをすることをお薦めいたします。
詳細は以下の技術情報をご参照ください。
ドリル加工でセンターもみつけが必要な理由 - 卓上ボール盤などの穴あけ作業では、切り屑により巻き込まれ事故が発生するので、軍手は着用しないでください。 切り屑がドリルにからまる場合、適時ステップ送りを行ってください。詳細は以下の技術情報をご参照ください。
ドリル加工のステップ量の目安 - 加工物の固定は確実に行なってください。
- ドリルの脱着時は、チャックから落下させてしまうことがあるので、テーブルの上にあらかじめウエスなどを敷いておくことをお薦めいたします。