「危なかった…」とヒヤリとしたことはありませんか?ヒューマンエラーの原因と、設計や保守の具体策をひとまとめ
- ヒューマンエラーの傾向/なぜ発生するのか
- 対策は?/ポップアウト効果/ホーソン効果
- ヒューマンエラー対策/最後に
設計者のヒューマンエラー対策
作業員の教育までが、設計者の仕事
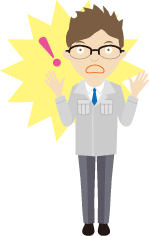
設計者が一番陥りやすいのは、「まさかこんな使われ方をするとは…」ということに気づかないことです。
装置を止めるために、作業員が日常的に非常停止ボタンを使っていたという話もあります。
設計は設計、運用は運用、保守は保守と分業されていますが、皆が設計概念を理解しているわけではありません。
そして、人件費削減や効率化により、広大な建屋に監視員が数人いる程度で、
紙のマニュアルを見ないと装置のことがわからないことも多くなりました。
また、最近は工場の海外進出も増えています。マレーシアの工場でも、
作業員は出稼ぎのバングラディッシュ人やネパール人で、言語もばらばらです。
このような状況を踏まえ、設計者も装置を作るだけでなく、教育まで考える必要があります。
マニュアルも、写真や絵を多用したり、一方的に読むことを強要するのではなく、
動画で20分見ればわかるようにしたり工夫します。
人間は、直感でわかるもの以外は、覚えられないということを常に考えておくことが大切です。
教育に加え、安全検証という考え方も大切です。
これまでは、事故に対して、対策を打つという前例主義でした。これからは安全を実証することが求められています。
全てのリスクをあげることは難しいので、主なリスクを数十個レベルで列挙します。
そして、その全部のリスクを防護していきます。
保守のヒューマンエラー対策
装置への責任者を決めて、情報を集約する仕組みを作る
最も理想的なのは、設計、運用、保守・検査が分離していることです。
しかし、一般的な会社では一緒となることもあります。
大切なのは、保守担当者が異変に気づいて、それを正常に戻すように意見が言えるということです。
1985年に起きた日本航空123便墜落事故は、修理ミスが原因と言われています。
客室乗務員の間では、すきま風がする飛行機だと言われていましたが、この情報は活かされませんでした。
この反省を元に、航空機業界では「機付整備士」という制度ができ、
その機体に関する情報は担当整備士に集約する仕組みができました。
そして、傷跡のデータベース化も行い、整備士が、万が一の時は異変に気づける体制になっています。
マニュアル通りに作業をするのではなく、いろんな部署や人からの情報をキャッチすることが大切です。
最後に
特集の最初で紹介した食品工場での配合、加工間違いの対策をご紹介します。
原材料の配合間違いを防ぐには、検査工程を設け、攪拌機の横にトレーを置き、
そこに原料を全て置いてから正しいかどうか確認してはじめて、投入します。
節目や関所を置くという考え方が肝心です。
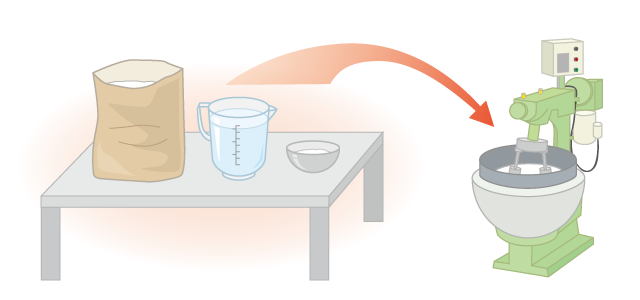
検査が作業に従属する流れになる場合、検査担当者のローテンションが効かず、間違いを発見できません。
作業を忘れると検査も忘れてしまうという可能性があるので、注意が必要です。
取材協力
- 独立行政法人 産業技術総合研究所 中田亨 主任研究員、博士(工学)
参考文献
- 仕事の段取りべからず71 JIPMソリューション 中田亨著
- 「事務ミス」をナメるな! 光文社 中田亨著
- Harvard Business School and the Hawthorne Experiments (1924-1933)