① 設計プロセスとは何か
設計とは、必要とする機能を具現化し検討した結果を工業製品や建築物、情報システム等を造るために仕様(設計図書)や設計図・設計書などを作る作業と定義されています。
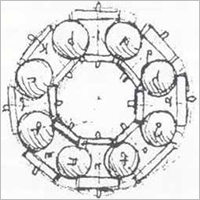
図1 レオナルド・ダ・ヴィンチ考案の
ベアリング
大昔の設計では、15世紀にレオナルド・ダ・ヴィンチのベアリング構造図(図1)が事例に挙げられますが、この時代の設計は、初歩の力学と使用する素材特性程度を考えながら、機能具現の構造を設計していたと思います。
その後は、工学分野の発展とともに実証実験的な手法で工業製品が設計されますが、コンピューターが普及する時代から、工業製品の設計プロセスが大きく変化します。 1)
② 設計プロセスとCAD
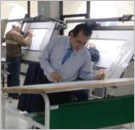
図2 手書き製図の写真
CADが開発されるまでは設計図は、ドラフターを使った手書き図面でした(図2)。この時代は、図面修正が非常に手間のかかる作業となるため、ベテランの設計技術者は図面を書き初める時に完成図面を想像して全体配置を決めることで、製図の修正を最小限にする能力がありました。
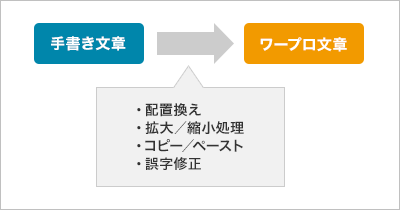
図3 2D-CAD効果の例え
しかし、CAD(2D)が社会に普及する1980年代になると、設計技術者は、設計ミスによる修復作業の煩雑さに大きく悩まされることが無くなり、製図作業の高効率化の恩恵を得ました。これは、手書き文章がワープロ文章に変わった効率化に例えることができます(図3)。しかし、設計者の能力強化に大きく貢献した変化ではありませんでした。
1990年代後期からの半導体技術の高度化により、工業製品は製品とその生産の両面で大きな変革が起こり、その後グローバル競争時代となりました。この世界規模の産業界における環境の大変革への対応には、「2D-CADがもたらした設計作業の効率化」では競争優位が確保できる設計支援ツールとはならず、「3D-CADを活用した開発・設計プロセス」が決定的な優位さを持つ設計支援ツールとなってゆきます。
即ち、この段階の設計プロセスは、一世代前の設計プロセスとは根本的に異なる知的作業を伴う開発・設計プロセスに変化し、設計品質だけでなく時間・距離・一貫性・フレキシビリティなどの競争優位性を競う状況にドラスティックに変化します。具体的には、3次元で構造化された製品構造データを用いて、
- ① 構造強度
- ② 熱伝達特性
- ③ 成形プロセス解析(樹脂流動性など)
- ④ 組立作業性評価
など、多岐にわたるシミュレーション解析(例:図4)を実施した上で最適な生産用治具やツール類の設計支援ができる様になります。更に3D-CADの威力は、2D-CADでは設計できない曲線を持つ立体構造(例えば、自動車ボディなど)の外形設計(座標定義)が精密にできることで、その結果、3D-CAE(シミュレーション)を経て構造化が決まると、3D-CAMによる切削加工にデジタルデータが活用でき、その加工品を3次元測定器で計測した外形データと設計データとを比較評価(3D-CAT)することができます。この様に、机上の最適化設計のエンジニアリング作業から加工、計測までを含むトータルエンジニアリング支援ツールとなりました。(図5)
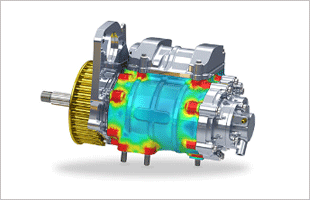
図4 3D-CAEの事例 2)
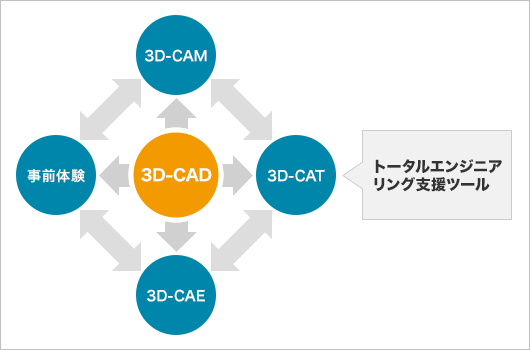
図5 3D-CADシステムによるトータルエンジニアリング支援ツール効果
第2回では、3D-CADシステムの更なる進化の現状について解説します。
注):本コラムでは、CAD=設計支援ツール、CADシステム=CADとそのデータを活用したCAM、CAEなどを含む支援ツール、として区分しています。
参考文献
- 1. Wikipedia:設計
- 2. ダッソー・システムズHP、シミュレーションより